Die reale Fabrik in der virtuellen Welt abbilden
Wo gibt es Bremsklötze in der Produktion? Welche Anpassungen in der realen Fabrik bringen Vorteile?
Diese und weitere Erkenntnisse lassen sich aus dem Service „Virtual Factory“ des ONCITE Digital Production System ziehen. Es ist der digitale Zwilling der Produktion und dient der Akquise, Darstellung und Analyse von Daten aus der Fabrik. Mit dem Service „Virtual Factory“ können sich Produktionsbetriebe wandlungsfähiger und effizienter aufstellen. Durch die Möglichkeit, die Fabrik mittels 3D-Visualisierung in near Realtime abzubilden, lassen sich schnell potenzielle Engpässe oder Störfaktoren identifizieren. Das ermöglicht es, die Produktionseffizienz und -flexibilität zu erhöhen.
Key-Features
- Status der Produktion schnell und einfach in 3D abbilden.
- Dashboards einfach erstellen – zur Kombination aus Visualisierung und Widgets mit Daten.
- Individuelle Mini-Dashboards direkt am Objekt sowie detaillierte Dashboards im BI-System nutzen.
- Daten (vom Sensorwert bis zur ERP-Buchung) nahezu in Echtzeit erfassen und sammeln, um Einblicke in near Realtime erlangen zu können.
- Historische Darstellungen – zum Bsp. zur Erkennung von Störfaktoren – generieren.
- Anomalien feststellen und in Korrelation bringen.
- Eingehende Datenanalyse vornehmen: von der einfachen Aggregation zur Erstellung von Berichten bis hin zur Data Science-Anwendung.
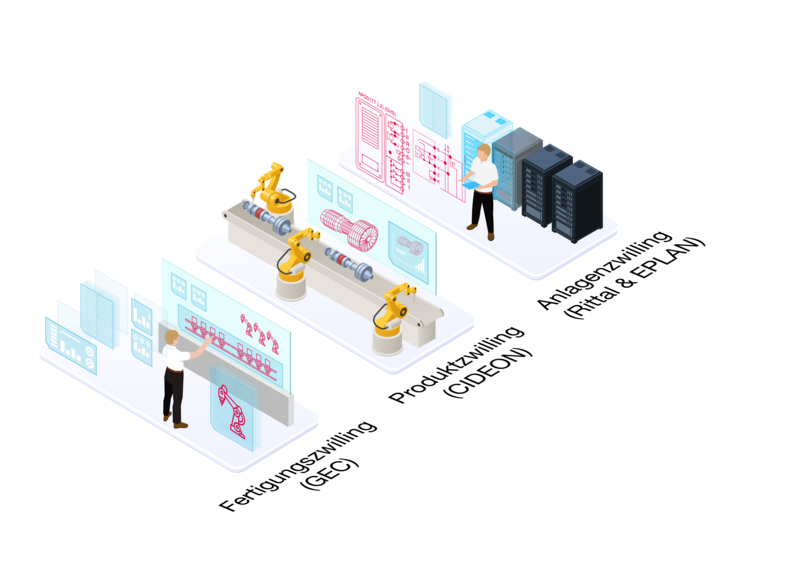
Potenzielle Engpässe oder Störfaktoren schnell identifizieren
Erhöhen Sie mit dem Service der Virtual Factory Ihre Produktionseffizienz und -flexibilität.
Digital Twin im Werk Haiger
Das Rittal-Werk in Haiger, zeigt, wie die Virtual Factory in der Praxis funktioniert.
Hier wurde mit der ONCITE Virtual Factory der Digitale Zwilling für die Produktionslinien umgesetzt. Der integrierte ONCITE Software-Service fungiert als zentrale Datendrehscheibe und sammelt die massenhaft anfallenden Daten der verschiedensten Sensoriken ein, harmonisiert diese und stellt sie als Digital Twin für Datenanalysen zur Verfügung. Das ONCITE DPS stellt auch das 3D-Modell der Produktionslinie bereit. Die laufend generierten Sensordaten (reale Zustandssicht der Anlage) werden an dem virtuellen Abbild der jeweiligen Anlagenkomponente angezeigt. Entstehen Probleme, sind diese sofort sichtbar. Das System sendet die Daten parallel in near Realtime für detaillierte Analysen weiter. Mit stetig wachsenden Datenmengen können die optimalen Produktionskennzahlen ermittelt und auch kleinste Abweichungen erkannt werden.
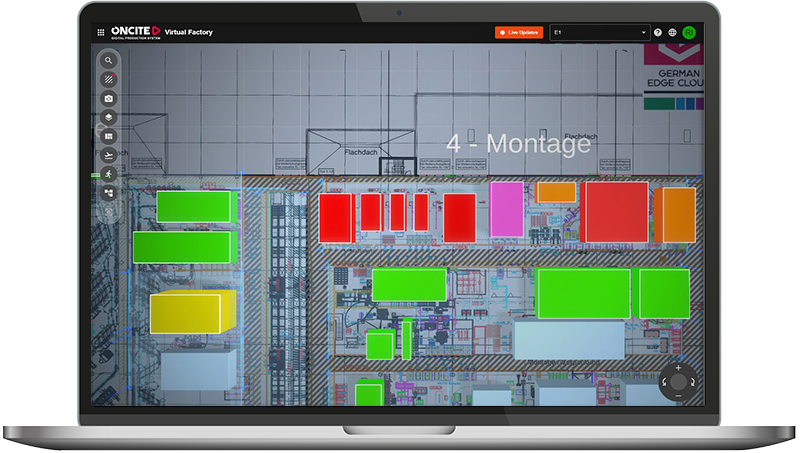
Im besten Fall lassen sich die Abweichungen vollautomatisch über den geschlossenen Regelkreis korrigieren – hin zu einem „Data Driven Automation“-System. Mit diesen Zyklen wird die Lernkurve der Anlage angereichert und stetig gemäß Machine Learning verbessert. Die in dem ONCITE DPS verfügbare IoT- bzw. Low-Code-Development-Plattform bringt alle Produktions- und Prozessdaten an einen Ort. Sie vernetzt, sammelt und bereitet die Daten auf. Dabei harmonisiert sie die heterogenen Daten, überführt sie in ein standarisiertes Industrie-Datenmodell und verdichtet sie zu wertvollen Informationen.
Aus dieser validen, strukturierten und normierten Datenbasis bedienen sich über komfortable API-Zugriffe diverse Services, die zu einem großen Teil ebenfalls Bestandteil des ONCITE DPS sind. Mit der Kombination von IIoT- und Produktionsdaten lassen sich komfortable Datenanalysen erstellen oder beispielsweise Zustandsverläufe der Maschine in einem frei definierten retrospektiven Zeitraum in Verbindung mit den Sensordaten anzeigen und auswerten.
Digitale Zwillinge clever vernetzen
Die heutigen Herausforderungen der Industrie können nicht isoliert betrachtet und gelöst werden.
Es gilt daher, die Welten Anlage, Produkt und Fertigung übergreifend miteinander zu vernetzen und Prozesse digital gestützt zu optimieren – zum Beispiel auch in Richtung Energieverbräuche. Dazu muss für Anlage, Produkt und Fertigungsprozesse je ein vollständiger digitaler Zwilling erzeugt werden. Diese müssen anschließend klug verbunden werden. Wie das gelingt und welche Vorteile das bringt, das zeigen German Edge Cloud, Rittal, Eplan und Cideon in einem Use Case.
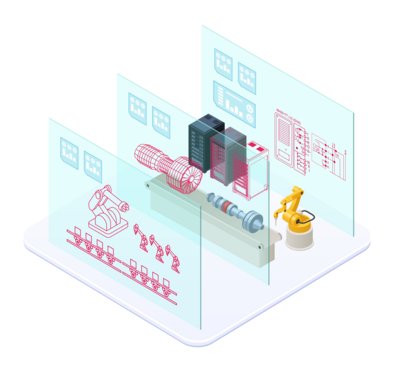
Smart Factory Apps
Einfache Integration von Software-Services für die bedarfsgerechte und kostenbewusste Produktionsoptimierung.
Energiemanagement
Transparente Analyse und Aufzeichnung der Energieverbräuche in der Produktion – für mehr Effizienz und Nachhaltigkeit.
Low-Code Application Development
Die komponierbare Architektur garantiert mehr Agilität und maximale Resilienz im Zeitalter der IoT-Lösungen.
Industrial IoT
Dank konsolidierter Daten die Produktionsprozesse im Überblick behalten – für mehr Erkenntnisse und faktenbasierte Entscheidungen.